Foundation Design Wayne C Teng Pdf To Excel
Documents Similar To Foundation Design - Wayne C Teng. Viggiani C., Piles and Pile Foundations, 2012.pdf. Tomlinson Foundation Design and Construction. More From Anonymous lMTMFfmPl. Skip carousel. Carousel previouscarousel next. Elastic-Settlement-Shallow-Foundations_A-Critical-Review-2.pdf Soilmechanics Ufc 2005 Educ Portal Rootgrowth Auf TEVI GIULIANO Controlul Geologic Al Poluantilor unsicherheit in der geotechnik.pdf 0946273 UfukErgun_ppr.pdf.
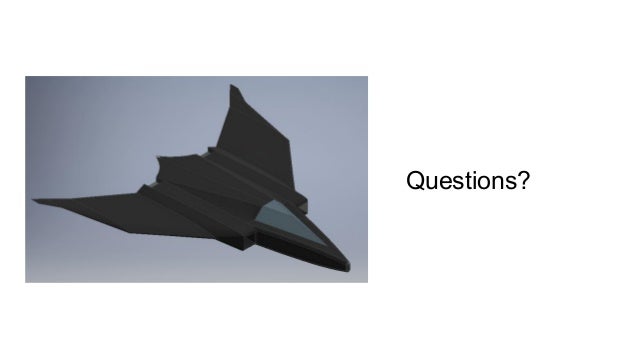
Download Welcome to the Civilax Virtual Library, the most comprehensive online civil engineering resource collection in the world.Here you can explore Structural Dynamics and Earthquake Engineering Books. Details Number of Books: 538 e-Books Format:.PDF,.DOC,.djvu Size: 9.45 GB Download: Direct Download in zip format (400mb parts) Read Online: Available in Civilax Cloud Storage to Read Online Special Notes All books are named with its original titles for the convenience of users.
All books can be read online All books can be downloaded one by one or as a complete set. Download: Welcome to the Civilax Virtual Library, the most comprehensive online civil engineering resource collection in the world.Here you can explore Structural Analysis and Design Books collection from our Virtual Library. Details Number of Books: 731 e-Books Format:.PDF,.DOC,.djvu Size: 11.5 gb Download: Direct Download in zip format (400mb parts) Read Online: Available in Civilax Cloud Storage to Read Online Special Notes All books are named with its original titles for the convenience of users. All books can be read online All books can be downloaded one by one or as a complete set. How can I design a reinforced concrete flat plate in SAP2000? Expanded Question: When I model slabs (or shell elements) using FEM software, the usual output is the contour plots on the shells which are not very useful for designing. Is there any way I can design a plate element (for example a flat plate) using FEM program?
Answer: For a number of years what I have been observing is that most of the time the design reports include contour plots for the shell elements for different load combinations. These contour plots a not useful to have a quick insight on the analysis results. Hence presenting the contour plots in the design reports is not a good practice. A way out is to use section cut techniques which are available in most of the FEM packages.
We can defined the section cuts according to the strips defined in the ACI 318 code. The output for the strips shall be the more familiar bending moment and shear force diagram plotted along the length of the strips. An extra advantage of the diagrams will be that a diagrams (bending moment, shear force and axial force) for different load combinations can be drawn on one plot simultaneously, hence easy to determine the governing load combinations.
Note:- FEM package like SAFE has built in features similar to section cut, that’s why you get analysis results for strips. Example Consider a reinforced concrete flat plate rested over 3m high columns. The structure consists of two bays in x-direction and two bays in y-direction. The bay width in x and y-directions is 5m. The slab thickness is 175mm.
The column size is 500mm square. The slab is loaded by self weight of the slab and live load of 5 KN/m2. Design the flat plate using section cut techniques in SAP2000. (Since the flat plate is symmetrical in two directions, one needs to define section cuts in one direction and for half the slab) Figure 1: Example reinforced flat plate with the section cuts marked for column strips and middle strip Explanation The slab can be divided into column strips and middle strips, according to the ACI-318 code. Since the flate plate is symmetrical in two directions, one needs to define strips in one direction and for half the slab. Hence two column strips and one middle strip is marked on the figure 1.
Now the section cuts are to be defined to capture the total force (Shear force, bending moment and axial force) in the width of the strip. For this purpose, 5 section cuts are to be defined in each span for each strip (10 section cuts per strip). The section cuts are numbered in the figure 1. One can use the option Draw ->Section cut. But the output is not saved for future use, if this option is used. There is another way to define section cuts using Define ->Section cuts By using the Define ->section cut option the output for the forces on the section can be recalled and processed later on. The section cut has to be defined using Quadrilateral cutting plan.
It is preferable that the cutting plane be kept slightly away from the nodes, because sometimes SAP2000 is unable to process the output for the section cuts exactly at the nodes, and report a zero values. Figure 3 shows the data for section cut definition for column strip 1 for section cut #1. Note that the slab is at elevation 3m in z-direction. Therefore the cutting pane is defined such that the slab is cut by the plane.
Figure 2: Define section cut dialogue box Figure 3: Section cut definition for column strip section cut #1 Similarly 10 section cuts are defined for each strip. The output for the section cuts can be called for all the load cases and combinations and processed. Using the menu Display ->Show Tables ->Structure Oputput ->Other Output Items ->Section Cut Forces Analysis, the section cut forces can be displayed Figure 4: Section cut forces display Figure: 5 Section cut forces The section cut forces can be exported to Excel by using Export current table ->To Excel option In Excel the forces diagram for the strips can easily be drawing for any load combination by little processing of data. For this example M22 gives the bending moment about y-axis, and F33 gives the shear force along the length of strip. The outputs for the three strips are given in Figures below Figure 6: Bending Moment and shear force diagram for Column strip CS1 Figure 7: Bending Moment and shear force diagram for Column strip CS2 Figure 8: Bending Moment and shear force diagram for Column strip MS1 NOTE Always cross check the forces resulting from Section Cut. The sign of the forces at most of the occasions has to be corrected manually.
(This is pretty easy to do). You have to take care that what section forces report you need on the right and which sections should report on the left. After running the structural models they create numerous analysis files with very strange file extensions.
Here I am talking about CSI softwares; ETABS, SAFE and SAP. These analysis files contain information about matrices and analysis results. More information about the file extensions can be found on CSI official webpage: or When sending the model files to someone you dont need all those temporary analysis files rather just 2 files; one model file and another its text file. Why we need to delete the files? Well, one thing is there are lot of files which we dont recognize, and the major issue is they take too much of space.
A single model may be upto 10MB or less or more, but after analysis, the folder size reaches sometimes upto 1GB, using hard disk resources. So its not wise to just leave them as is because once you have model file you can get the results on any machine after running it. For example for a simple model! An increase of about 62 times! Deleting the Files 1) From program To delete the analysis files of the model, there are many ways and techniques:- Open the model, goto File>Delete analysis files>There are 2 options; one for deleting analysis files of that model only and another to delete files of all the models in that specific directory.
Here it can’t delete the files of models in sub directories. Just imagine if you have a large project containing many buildings having at least 2 models, all in separate directories, so would have to open all of them one by one and delete files this way.
2) Manually Deleting the Files Another method is to search and delete the files yourself. Unfortunately, I could not find on internet a complete list of all the extensions of analysis files. So I just created sample files for each of the program and then converted by some means those extensions into a text file. I will for your convenience put all those extensions here. So just goto windows search explorer and just copy paste the extensions text string the file name box of search window and delete all the files in one go. If I have missed some extensions of mixed it with other programs, please correct me. 3) The best method While writing this article, I came across a very interesting method to do all that crap.
There is file calledEat.bat in ETABS and SAP program files. When I opened these files in MS DOS, I found out that this DOS files deletes all the analysis files in that directory and you can get the list of all the extensions of the files if you try to edit it. Well that would be the official extension list of analysis files from CSI. The extensions I published below were extracted by me so they miss some extensions.
I will later update those. This Eat.bat is found in ETABS and SAP folders but not in SAFE. I dont know why CSI people havent included this in SAFE. So I came up with an idea to modify the program so that it can do following:- 1) Delete all the analysis files, not just in that specific directory rather in all sub directories too and for all programs like ETABS, SAFE and SAP.
I will just add all the extensions and a switch for deleting files inside other directories:- ERASE /S /Q * Soon it will also be available in standard EXE format. Autodesk Revit - a program for the design and construction of buildings and structures. Autodesk Revit based on the technology of information modeling of buildings and is intended for the design and management of data on buildings and structures at all stages of construction. Project ideas are embodied in it a reality thanks to the coordinated and consistent model-based approach.
Autodesk Revit - a complete solution that combines the capabilities of architectural design, design of engineering systems, building designs and construction simulation. The innovative and revolutionary new ETABS is the ultimate integrated software package for the structural analysis and design of buildings.
Incorporating 40 years of continuous research and development, this latest ETABS offers unmatched 3D object based modeling and visualization tools, blazingly fast linear and nonlinear analytical power, sophisticated and comprehensive design capabilities for a wide-range of materials, and insightful graphic displays, reports, and schematic drawings that allow users to quickly and easily decipher and understand analysis and design results. From the start of design conception through the production of schematic drawings, ETABS integrates every aspect of the engineering design process. Creation of models has never been easier - intuitive drawing commands allow for the rapid generation of floor and elevation framin Driver Atx V2 X Support Download. g. CAD drawings can be converted directly into ETABS models or used as templates onto which ETABS objects may be overlaid. The state-of-the-art SAPFire 64-bit solver allows extremely large and complex models to be rapidly analyzed, and supports nonlinear modeling techniques such as construction sequencing and time effects (e.g., creep and shrinkage). ETABS 15.2.2 Enhancements • Shear-Wall Design Report- Eurocode 2-2004 enhancement to report wall unbraced height used for computing pier buckling load capacity.
• Slab/Beam Design - CSA S16-09 and CSA S16-14 enhancement limiting the total effective width of the slab to 1/4 the span of the beam and taking in account the amount of deflection caused by shrinkage of the concrete. • Material Library - Russian material library updated. Output and Display. I would recommend this book to every structural engineer. Very easy, precise and concise. I am so in love with this book that I would like to thank the author; Ian A MacLeod for sharing with us this tremendous, sheer amount of knowledge and wisdom about modelling process.
I have developed a flow chart and a short summary out of the chapters related to modelling process to share with you. The process discussed here is advocated in IstructE (2002), MacLeod (1995), NAFEMS (1995, 1999) and ISO 9001 (2000). It tends to be used in a formal way by those who specialise in analysis modelling. By formal is meant that a written record of the activities always be adopted in order to reduce risk in analysis modeling. The degree of understanding gained from doing hand calculations is normally overestimated.
Reflective consideration of results is a more fruitful source of understanding than arithmetical processing. Engineers were concerned that the introduction of computers would result in dumbing down of engineering. ‘Monekys’ could be trained to hit the right keys. While there is a significant danger that software can be used in the absence of competence, the reality of computer use for modelling is that it has made the work more intellectually challenging. To operate successfully in environments of significant uncertainty requires intellectual power of the highest order. This is the realm of modern structural analysis – the realm of the professional engineer.
Risk is defined as the combination of the likelihood and the consequences of an event which can cause harm. The likelihood of occurrence of a disaster due to structural analysis modeling is low but the potential consequences from such an event are severe. The risk of a disaster causing serious harm due to inadequate modelling cannot be eliminated; it can only be minimised.
But to be minimised, the modelling process needs to be formally adopted. There are two basic processes in structural analysis; 1-Model development process 2-Solution process Traditionally, the model development process was a minor issue but today, the emphasis for the structural engineer has changed radically from analysis to model development. The paradigm shift has not been identified in education and hence it is not well understood in practice. Following tables gives the comparisons between the skills needed in practice and skill given in education.Modelling process (as explained in theory and in the given flow chart) can be interpreted as implying a linear implementation, the real process is likely to involve much looping back to previous stages. ETABS is an engineering software product that caters to multi-story building analysis and design. Modeling tools and templates, code-based load prescriptions, analysis methods and solution techniques, all coordinate with the grid-like geometry unique to this class of structure.
Basic or advanced systems under static or dynamic conditions may be evaluated using ETABS. For a sophisticated assessment of seismic performance, modal and direct-integration time-history analyses may couple with P-Delta and Large Displacement effects. Nonlinear links and concentrated PMM or fiber hinges may capture material nonlinearity under monotonic or hysteretic behavior. Intuitive and integrated features make applications of any complexity practical to implement. Interoperability with a series of design and documentation platforms makes ETABS a coordinated and productive tool for designs which range from simple 2D frames to elaborate modern high-rises. Theoretical basis for response spectrum calculations in spectral analysis Understand that the method of determining response spectrum Sa=Sa(T) for a given diagram of accelerations F(t), where T refers to period, Sa refers to acceleration spectrum, t refers to time, while F(t) is a given time analysis function. This is useful if in comparing the seismic responses obtained with the use of both spectral analysis and time analysis.
The curve of response spectrum Sa=Sa(T), that overlaps exactly with the given function F(t) of time analysis (saving the acceleration diagram) should be ascribed. You can analyze the dynamic structure response using the method of response spectrum (spectral analysis) for the current acceleration diagram. The pseudo-spectral acceleration is the maximum acceleration of a single degree of freedom due to the given diagram of acceleration. How is the plane of the section cut defined when drawn in a 3D view? Expanded Question: When a section cut is drawn in a 3D view, only the X and Y coordinates are provided. How is the section-cut plane defined?
Answer: When using the Draw >Draw Section Cut command, forces are reported in the section-cut coordinate system which is defined by three axes (1,2,Z) as follows: • Section-cut 1 axis is located within the plane parallel to the global X-Y plane, and rotates counterclockwise from the global X axis according to the user-defined parameter Angle (X to 1). • Section-cut 2 axis is also located within the plane parallel to the global X-Y plane, though it is oriented 90° counterclockwise from the section-cut 1 axis. • Section-cut Z axis is parallel to the global Z axis. Integrated forces are reported either on the left or right side of the section cut, according to the right-hand rule.
Take, for example, a section cut drawn from left to right along the horizontal plane within a X-Z view. Integrated forces on the left side represent behavior above the section cut, while those on the right side, below. Using the right-hand rule, these forces are expressed in the section-cut coordinate system (1,2,Z). Why are section-cut integrated forces shown in 1,2,Z and not 1,2,3 directions? Answer: For section cuts drawn within the graphical user interface, the section-cut 3 axis is always parallel to the global Z axis, therefore integrated forces are shown in 1,2,Z directions since this notation is more precise. Why is the magnitude of integrated forces different for the left and right sides?
Expanded Question: According to equilibrium, should not the magnitude of integrated forces be equivalent for both left and right sides? Answer: Section-cut forces may be different on either side of a section cut because they are based on joint forces which occur in the global system.
Globally, these forces are in equilibrium, but their relation to a section cut is arbitrary and does not necessarily serve the function and conditions of a free-body diagram. As an example, consider a section cut located in the middle of a cantilever beam modeled by a single frame element and loaded by its self-weight only. The results on the side of the section cut that includes the fixed end will represent the beam reactions, while the results on the side of the section cut that includes the free joint will be zero. Example of Section cut Expanded Question: Consider a cantilever beam made of solid elements. Figure below shows the beam with the unit (1lb) load at the end of the beam. The global axes are also displayed for reference.
(Note:- Example 5-002 of the verification manual of SAP2000 v 14.1.0 is used here) Hand calculations shows Max. Shear force = 1lb Max.
Bending moment at support = 1 x 6 = 6 lb-in Stress = 6 x 0.1 / (0.1 x 0.23 /12) = 9000 psi Figure 1:- FEM model of cantilever beam with unit load at the tip. Figure 2 shows the longitudinal stresses in the beam. The maximum stress of 9000psi is shown near the support. Figure 2:- Longitudinal stresses in the beam subjected to unit load in z-direction at its tip. Draw a section cut near the support to determine the bending moment keeping in mind the orientation of axes of section cut as explained above. Display the beam in xz-view to draw the section cut conveniently.
Zoom near the support as the forces are desired near the support. Draw a section cut line near the support. Now adjust the coordinates of the start and end of the line to adjust the line at 0.05” from the support and is parallel to the z-axis.
The location of the resultant is to be adjusted to the desired location. We need to output forces at mid height of the section so that bending moment is integrated about the mid of the section. Adjust the ‘X’ of resultant to desired location. For this beam the width is 0.1”, so put 0.05” to be at mid of the width. Adjust ‘Z’ to mid height of section (Although in this example it will not affect the results). The most important here is to adjust the angle.
The Angle (X to 1) is the angle by which the 1-axis of the section cut is to be rotated counterclockwise from the global x-axis. The 1-axis of section cut is always in a plane parallel to the global xy-plane. The 2-axis of the section cut is 90◦ CCW from the 1-axis. For this example, if angle for resultant is put as zero, the ‘1’ axis will be in the direction of global x-axis. The ‘2’ axis will be into the paper. Hence the major bending moment will be about the ‘2’ axis.
The major shear force will be in the ‘Z’ direction. The results are displayed in figure 3. Figure 3: Section cut output and explanation.
Tekla Structures can be used with other existing applications, or solely as a platform to develop their own workflows. Open platform supports interoperability and standardization. Tekla Structures links with various systems through Tekla Open API ™ application programming interface that is implemented using Microsoft.NET technology. Example, Tekla Structures supports the following standard formats: IFC, CIS / 2, SDNF and DSTV. Tekla Structures supports proprietary formats such as DWG, DXF and DGN. The SAP name has been synonymous with state-of-the-art analytical methods since its introduction over 30 years ago.
SAP2000 follows in the same tradition featuring a very sophisticated, intuitive and versatile user interface powered by an unmatched analysis engine and design tools for engineers working on transportation, industrial, public works, sports, and other facilities. From its 3D object based graphical modeling environment to the wide variety of analysis and design options completely integrated across one powerful user interface, SAP2000 has proven to be the most integrated, productive and practical general purpose structural program on the market today.
This intuitive interface allows you to create structural models rapidly and intuitively without long learning curve delays. Now you can harness the power of SAP2000 for all of your analysis and design tasks, including small day-to-day problems.
Complex Models can be generated and meshed with powerful built in templates. Integrated design code features can automatically generate wind, wave, bridge, and seismic loads with comprehensive automatic steel and concrete design code checks per US, Canadian and international design standards. Tekla Tedds is powerful software to automate your repetitive structural calculations. Choose from one or more of our regularly updated calculation libraries or write your own, and create professional documentation every time. Combine your structural calculations with 2D frame analysis.
Tedds 2016 includes a new and fully integrated 2D frame analysis application along with many new and enhanced calculations to British Standards, Eurocodes and US, Canadian and Australian design codes. It is twice as fast as its predecessor and compatible with Microsoft Word 2016.
I've been looking for a reference as to how to determine the max soil pressure for a footing that has moments in both directions, but only has partial bearing. The moment in one direction would the load in the kern (if it were the only moment), and the moment in the other direction would put the load outside the kern. I can't find a reference on this in my foundations book, and I could go through the math of it (but that would take a REALLY long time, and I honestly don't want to spend an entire day to figure it out), but I figured someone else has to have done this before. My first inclination was to take the max pressure of the moment causing partial bearing and adding that to the max pressure caused by the full bearing (M/S), then I realized that I couldn't us the full S of the footing (for the smaller moment) because the whole footing isn't in bearing anymore.
I tried estimating the amount of the footing that would be in bearing and using that S. That would get me close, but I'm really trying to be exact because I'm evaluating a program.
The line of zero bearing stress is not perpendicular to either edge of the footing because of the moments in both directions, but again, I don't know how to address this without a day-long geometry session. RE: footing with biaxial moment (Structural) 28 Jan 09 09:37. As a first approximation, calculate the resultant moment acting on the footing, i.e. The vector sum of the two moments. Assume the line of zero pressure occurs parallel to the resultant moment (using the right hand rule). Take an educated guess where the zero pressure line is and determine whether the resulting stress block satisfies both load and moment.
Modify the position of the zero pressure line until load and moment are approximately satisfied. Then check the moment normal to the resultant vector. If it is not zero, modify the direction of the zero pressure line until it is close enough. Best regards, BA RE: footing with biaxial moment (Structural) 28 Jan 09 17:17. From personal experience, here are my views: 1. As suggested by MSQUARED48, avoid the situation to the best you can.
As JLNJ pointed out, use FEM with compression only spring. For personal satisfaction, you can write your own spreadsheet program assuming the footing and soil both are linear elastic (linear stresses). The difficult part is once a corner has developed negative pressure (uplift), the bearing area is reduced, and the new bearing area/neutral axes need to be found, its properties re-calculated (quite mathematically challenging), and load redistributed. The iteration process stops when the footing is fully in bearing. RE: footing with biaxial moment (Structural). There still seems to be something wrong with the results you guys are getting.
First of all, a 10'x10'x2' footing weighs approximately 30 kips. I don't know what you mean by 'an appropriate DL factor' but, for the sake of the problem, let us say that: P = 20k Mx = 88k-ft Assume that My = 0 for now.
The eccentricity in the x direction is 88/20 = 4.4', so for a 10'x10' footing, the effective length of bearing on the soil is (5 - 4.4)3 = 1.8' and the effective width is 10'. The soil pressure has a triangular distribution. Average pressure = 20/(10*1.8) = 1.11 ksf. Maximum pressure is 2.22 ksf. Minimum pressure is zero.
So far, we have said that My = 0. If My = 4k-ft, surely the maximum pressure will increase slightly, so the maximum pressure by my calculation is approximately 2.22 + 0.13 = 2.35 ksf. Am I misinterpreting the problem? Best regards, BA RE: footing with biaxial moment (Structural). Chicuck, No, there is no uplift on the footing. The axial load from the column (for the controlling load combination of 0.6DL-W is 2.818k. While the weight of the footing is 30k, you can only use 18k (because the load combination is 0.6DL-W), hence the TOTAL P=18k+2.818=20.818K (as noted in an earlier post).
I am not considering any soil overburden on the footing (whether that is right or wrong is irrelevant to what I am trying to do), I can specifiy overburden in the program, but all I want to do is verify that any situation that the program is faced with will be done correctly. BA, No, the max pressure is around 1.9ksf (for P=20.818, Mx=87.842k-ft, and My=4.226k-ft). RE: footing with biaxial moment (Structural) 30 Jan 09 10:25.
Using the revised values of 20.818k and 87.842k-ft, I would agree that the maximum pressure is in the order of 1.9 ksf. If the original values of 20k and 88k-ft are used, the maximum pressure is in the order of 2.35 ksf. This indicates that the footing is extremely sensitive to minor changes in load which suggests to me that this would be a very bad design, no matter what your computer program tells you. One point to note is that the factor of safety against overturning is only 20.818*5/87.842 = 1.185 which is completely inadequate by any standard. Best regards, BA RE: footing with biaxial moment (Structural). The AASHTO Code has a method for coming up with the qmax as well.
See Figure 4.4.7.1.1.1C in the 17th Edition. I am not sure if the same figure appears in the new one (LRFD only). I think it is strange that the code includes this figure because elsewhere in the code they do not permit bridge foundations to be loaded outside the kern.
On another note, we design sign and billboard foundations often enough, and it is entirely uneconomical to design a spread foundation with the resultant within the kern for wind load. It would irresponsible of an engineer to require the load to remain within the kern in such a circumstance. RE: footing with biaxial moment (Structural) 10 Feb 09 12:16. StructuralEIT- The 'S' used in the bearing pressure calculations, has no name, it's simply a variable defined by the formula. You're right, e y is 0.
To avoid dividing by zero, I've adjusted e y (and e x) by ε, as shown in the formulas on sheet 1. Ε is defined as.001 feet, but that definition is not shown anywhere on the printout. Px is the soil pressure at the center of the footing, if M x=0k'.
I use px to calculate the bending moment at the center of the footing, where I believe it is maximum. Again, I don't know where the soil pressure formulation comes from. I got it at least 20 years ago and have verified it against many other sources over those 20 years. It is always dead on. RE: footing with biaxial moment (Structural). Miecz- Thanks. Miecz and willis- Would it be possible for both of you to plug in the following loads in your respective sheets and tell me what you get?
Footing is 9'x9'x2' (but the self weight of the footing is already figured into P - using the 0.6DL factor) P=18.632K Mx=71.52k-ft My=5.646k-ft Using miecz's formulas I'm coming up with 2306psf (which is roughly what I would expect), but this program I'm checking is showing 3380psf (almost 50% higher). I found another method that I was trying out, but that's only giving me 1330psf (which is way too low, so I'm throwing that out).
RE: footing with biaxial moment (Structural) 10 Feb 09 14:15. With only P and Mx, the eccentricity is 3.84', or 0.66' from the edge of the footing. With a triangular distribution of pressure, the effective width of the footing is 3 * 0.66 = 1.98' and the maximum pressure = 2.09 ksf. Now, considering My = 5.64k' and a section modulus of S of 1.98*9^2/6 = 26.7 for the effective portion of the footing, the additional stress is M/S = 0.21 ksf. Adding the two together gives 2.30 ksf.
Best regards, BA RE: footing with biaxial moment (Civil/Environmental) 10 Feb 09 14:24. The AASHTO Standard Specs have Figure 4.4.7. 2005 Arctic Cat F7 Sno Pro Service Manual more. 1.1.1C to solve this kind of problem. It comes from the old AREA Railway Manual. It gives the same results, but, because it is a graphical solution, it gives information that formulas do not.
Specifically, with the loads and dimensions you have, the bearing pressure is very sensitive to small changes in vertical load or eccentricity. Just reducing P 6% to 17.56 kips raises the bearing pressure to 3380 psf. Could your program be fiddling with your input?
RE: footing with biaxial moment (Structural) 12 Feb 09 17:47. Here is one way to do it. On the attached sketch, Vol. Abcd is the volume under the stress block. Cx and Cy are measured from the edge of footing to the centroid of the stress block. H is the height at point a. Kh is height at point c.
0 is the height at b, c and e. Using Excel, one can experiment with different x and k values until Cx = A/2 - P/Mx and Cy = A/2 - P/My. Finally, calculate 'h' to satisfy the equation that the volume under the stress block is equal to P, the applied load. Best regards, BA • RE: footing with biaxial moment (Structural) 14 Feb 09 18:52. If anyone is interested, the RISAFoot program (even the free Demo version) provides information that can be used to verify a bi-axial soil bearing profile. That program will show you the soil bearing pressure at each of the 4 corners and will also display the distace from the point of maximum compression to the neutral axis location. If you know that information it is not all that difficult to verify that the total pressure load equals the applied vertical load.
I did this for one of our users yesterday. It takes me awhile to remember how to do the integration, but once I remember then it's not that bad. You can even use this same information to verify that the centroid of the soil pressure corresponds to the load eccentricity location. But, the integration gets more complicated, and I tend to 'guesstimate' it for my hand calculations instead. RE: footing with biaxial moment (Structural) 18 Feb 09 18:45. In the attached diagram, the pressure at corner b and d is zero.
The pressure at c is k times the pressure at a, namely h. The volume abcd is actually a truncated triangular pyramid, so can be expressed as abe - cde. The volume and centroid of a regular pyramid is well known, so no need to integrate. The procedure is to guess at x and k and iterate to a correct solution such that Cx and Cy correspond to the known location of the load P. When this has been found, the highest pressure, h (at point a) can be found by equating the volume of abcd to applied load P.
A bit messy, but it can be done. Best regards, BA • RE: footing with biaxial moment (Structural) 19 Feb 09 06:39.